The Client
The client transports over 100 million gallons of fuel daily from Houston, Texas to the New York Harbor with one of the largest refined products pipelines in the US. As a value-based energy company, it provides cost-advantaged, reliable, and environmentally sensitive solutions to meet customers’ needs and future energy demands. Committed to delivering energy that improves lives and keeps the economy moving, the company focuses on excellence in all its endeavors, continually raising the bar.
The client employs advanced corrosion prevention methods, such as cathodic protection and pipeline coatings, monitored using above-ground surveys to detect potential corrosion. They required a map-intelligent platform deployed across districts, covering all pipeline assets for proactive maintenance that was more efficient.
Need for enhancing pipeline inspections and maintenance
Energy and oil companies face significant challenges in maintaining the efficiency and reliability of their extensive pipeline networks. Current manual inspection and maintenance processes are labor-intensive and often disjointed, lacking integration with spatial data. This leads to delays in detecting issues such as corrosion, inefficient resource utilization, and reduced visibility into the overall condition of pipeline assets. Furthermore, the absence of real-time monitoring, advanced analytics, and automated workflows complicate decision-making and slows response times to critical situations.
To address these industry-wide challenges, companies need sophisticated, map-intelligent solutions that can automate inspections, optimize resource deployment, deliver actionable insights, and facilitate seamless team collaboration. Such solutions are essential for driving operational excellence, improving maintenance reliability, ensuring regulatory compliance, and minimizing unplanned downtime.
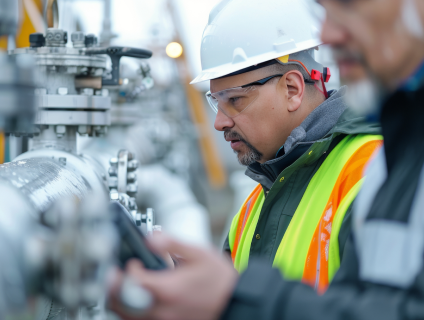
Challenges
The client faced several operational hurdles that impeded efficiency and effectiveness in managing pipeline maintenance and corrosion detection. Key challenges included:
- Labor-intensive inspections and surveys
- Lack of integration with spatial data
- Inefficient planning for field technicians
- Limited analytical insights
- Underutilized communication tools
- Lack of real-time monitoring and automation
These challenges necessitated an advanced, data-driven, and automated solution that leveraged geospatial technology to streamline pipeline inspections, boost operational efficiency, and ensure better corrosion prevention mechanisms.
LTIMindtree’s solution
LTIMindtree’s geospatial intelligent solution for survey operations and maintenance (GISSOM), introducing streamlined workflows and advanced technology features. It was deployed across all the client’s districts and it:
Implementation phases of GISSOM
Phase 0: GISSOM Set up
LTIMindtree’s proprietary GISSOM product was set up on Azure for preventive maintenance (surveys) and asset management.
Phase 1: Deployment and enhancements
Phase 1 application builds were deployed to districts south eastern district (SED), gulf coast district (GCD), and north east district (NED), covering all pipeline stretch assets. Bulk survey reading data imports were enabled via the GISSOM web application at flexible intervals. Atmospheric facilities were added as a new asset category, with parent-child relationships established between entities like facilities-assets and tanks-test points.
A calendar view streamlined survey scheduling, linking specific survey types (e.g., Rectifier PM, Inspections) to assets with distinct schedules. An automation workflow created tickets for high-priority issues, allowing manager comments and enabling self-assignment. Automated workflows for ticket management (assigning, resolving, escalating, and closing) and survey email notifications were also established.
Phase 2: Streamlined workflow enhancements with upgrades
We introduced several updates to optimize asset and maintenance management. Users could view and edit logic for static reports across surveys, maintenance, assets, and field engineers. Maintenance types and reasons were customizable by sub-category, and an atmospheric facilities maintenance workflow was implemented. Survey workflows accounted for a grace period on overdue dates, and new survey types were supported on the web application. Geo-tagged images could be captured during maintenance sub-ticket resolutions via mobile, with sub-tickets manageable on both web and mobile platforms.
A chat module facilitated communication between managers, admins, and field technicians, supporting file attachments, replacements, and file history viewing. Public and private report templates were introduced, allowing district-wide access for public reports and private ownership for individual users. Maintenance severity workflows included urgency attributes, ensuring more targeted prioritization.
Phase 3: Comprehensive system upgrades and new workflows
This phase involved integrating existing geospatial information system (GIS) datasets and migrating historic pipeline compliance system (PCS) data to create a robust data foundation. The ticketing system was upgraded to support the main and sub-tickets for Atmospheric facilities outside of surveys. An ask engine data directory was introduced, enabling users to query, analyze, and access actionable insights from relevant datasets.
Reporting was enhanced with tools to track data progression, improved custom report modules with search functionality, and overlay features to consolidate survey data, uncover trends, and highlight recurring issues
Application (GISSOM) tech stack
Web
Backend technologies | PostGreSQL + PostGIS, PgAdmin+ PgRouting |
Front-end technologies | HTML, Java Script, JQuery |
Programming Language | Java Script, OpenLayers |
Server |
|
Web API | PhP, c# (Scheduler) |
IDE | Visual Studio |
Mobile – Android
Backend technologies | SQLite |
Front-end technologies | XML |
Programming Language | Java, OSMdroid Library |
Library |
|
Web API | PhP |
IDE | Android Studio |
Mobile – iOS
Backend technologies | Core Data |
Front-end technologies | Storyboard |
Programming Language | Swift |
Library |
|
Web API | PhP |
IDE | Xcode |
Benefits
The implementation of GISSOM resulted in several benefits including:
Conclusion
In conclusion, LTIMindtree’s GISSOM solution empowered the client by enabling proactive asset and maintenance management, resulting in significant enhancements across multiple areas. By automating and streamlining various operations and workflows, the solution tripled inspection speed and boosted productivity. It provided a powerful, flexible, and user-friendly system that improved asset management, maintenance scheduling, and field operations, ensuring seamless management and enhanced productivity. For energy companies aiming to stay ahead, embracing innovative geospatial technology to optimize operations is the next crucial step in their digital transformation journey.
Looking to digitally transform your operations and maintenance with map intelligence?
Reach out to us at eugene.comms@ltimindtree.com.